Save Your Merchandising Costs by $50k+ a Year
As your merchandise business grows, cost optimization becomes a critical factor,
especially when dealing with the intricacies of the supply chain.
While the initial instinct might be to find lower-priced suppliers or negotiate with existing ones,
this approach often leads to unforeseen challenges. Factories may cut corners or
increase hidden costs, ultimately compromising product quality or delays in production.
The consequences can include order losses, batch complaints, negative customer reviews, and damage
to your reputation.

We'd like to introduce a fresh perspective on cost reduction while maintaining high-quality standards.
Imagine managing over 50 projects simultaneously across various product categories
plush toys, figurines, clothing, pins, and more. Different teams, multiple suppliers, designers,
finance, and logistics all play a role.

Now picture the information overload: design drawings,
product quotes, sample images, modification feedback, washing labels, purchase order details,
invoices—all scattered across emails, Google Drive, and other software. It’s like untangling a messy yarn ball, and if an
employee takes a break or leaves permanently (no blame there!), finding critical information becomes even harder.
The Traditional Factory Collaboration Process: Flaws and Challenges
1. Lack of Communication Efficiency:
People spend unnecessary time syncing information and resending files.
Vital details get lost in the shuffle, leading to confusion and delays.
2.No Big Picture View for Managers:
2.No Big Picture View for Managers:
Managers struggle to get a comprehensive overview of all ongoing projects.
This lack of visibility hampers effective production planning.
This lack of visibility hampers effective production planning.
3.Training and Handover Difficulties:
New employees require extensive training due to complex processes.
New employees require extensive training due to complex processes.
When someone leaves, knowledge transfer becomes a daunting task.
4.Tracking Issues and Mistakes:
4.Tracking Issues and Mistakes:
Without a streamlined system, mistakes increase.
Longer production times, project delays, and wasted manpower result.
Longer production times, project delays, and wasted manpower result.
The Solution: Enterprise Resource Planning (ERP) System
An ERP system streamlines communication across the entire production chain. Here’s how it works:
Sample Orders:
Each sample corresponds to a single page within the system.
This page contains design drawings, sample images, quotations, and other relevant details.
No more digging through scattered emails or folders!
Bulk Orders:
Similarly, each bulk order has its own dedicated page.
Details include product specifications, quantities, estimated delivery times, and more.
Managers can easily track progress and plan production efficiently.
Finance Integration:
Every sample and bulk order links to a corresponding invoice.
This simplifies verification and ensures accurate financial records.
Our Experience and Cost Savings
Our merch solution business has spent 7 years refining this system. We’ve digitized everything—
from client interactions to sample room management and production. The result? Significant cost savings—
at least $50,000 USD annually!
Get Started
If you’re interested in manufacturing merchandising items with us (such as plush toys, vinyl figures, or t-shirts),
our system is freely available. Feel free to reach out to us for more information or to explore our production catalog.
Remember, with the right system in place, you can save costs without compromising quality. Happy merchandising! 🛍️🌟
As your merchandise business grows, cost optimization becomes a critical factor,
especially when dealing with the intricacies of the supply chain.
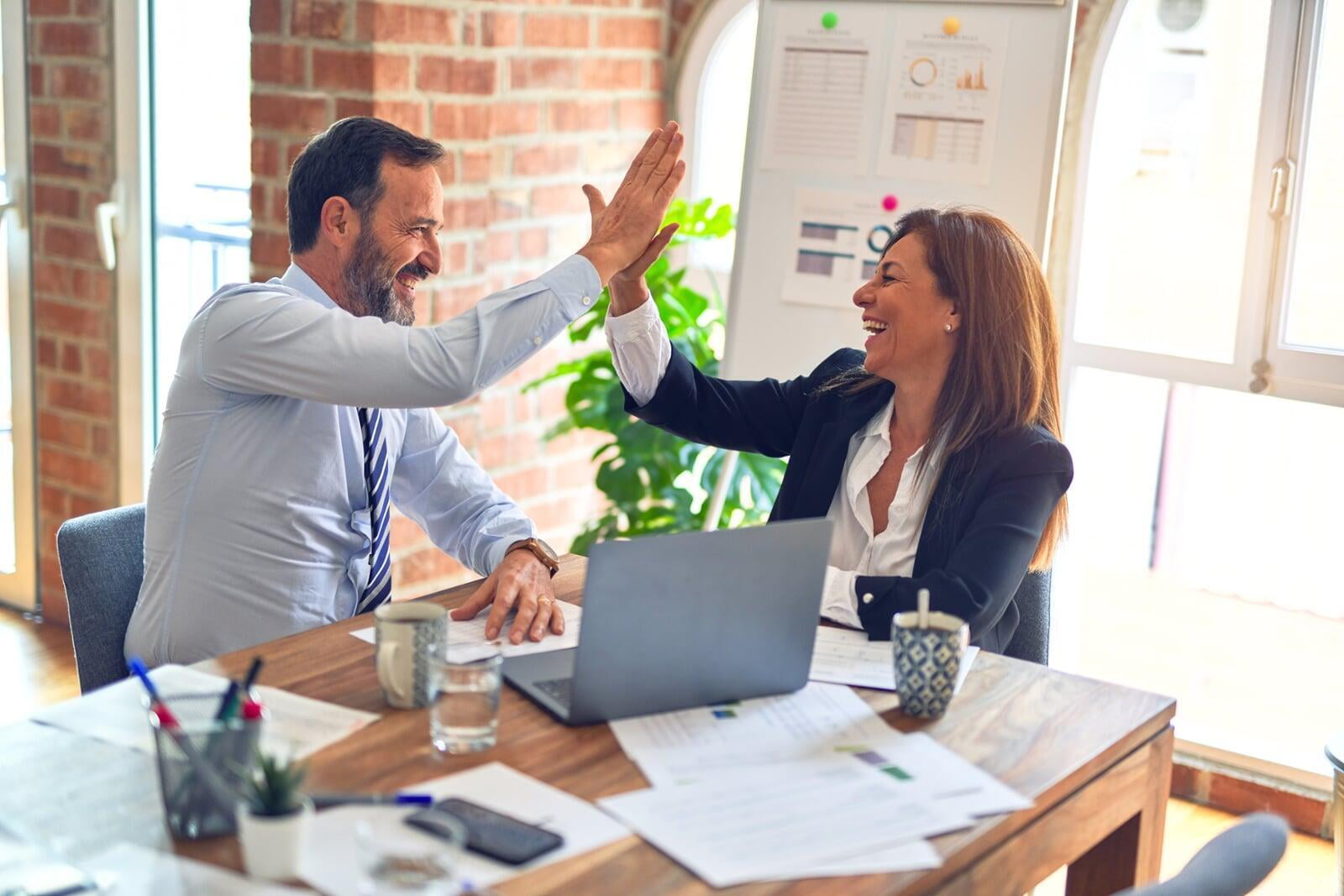
While the initial instinct might be to find lower-priced suppliers or negotiate with existing ones,
this approach often leads to unforeseen challenges. Factories may cut corners or
increase hidden costs, ultimately compromising product quality or delays in production.
The consequences can include order losses, batch complaints, negative customer reviews, and damage
to your reputation.
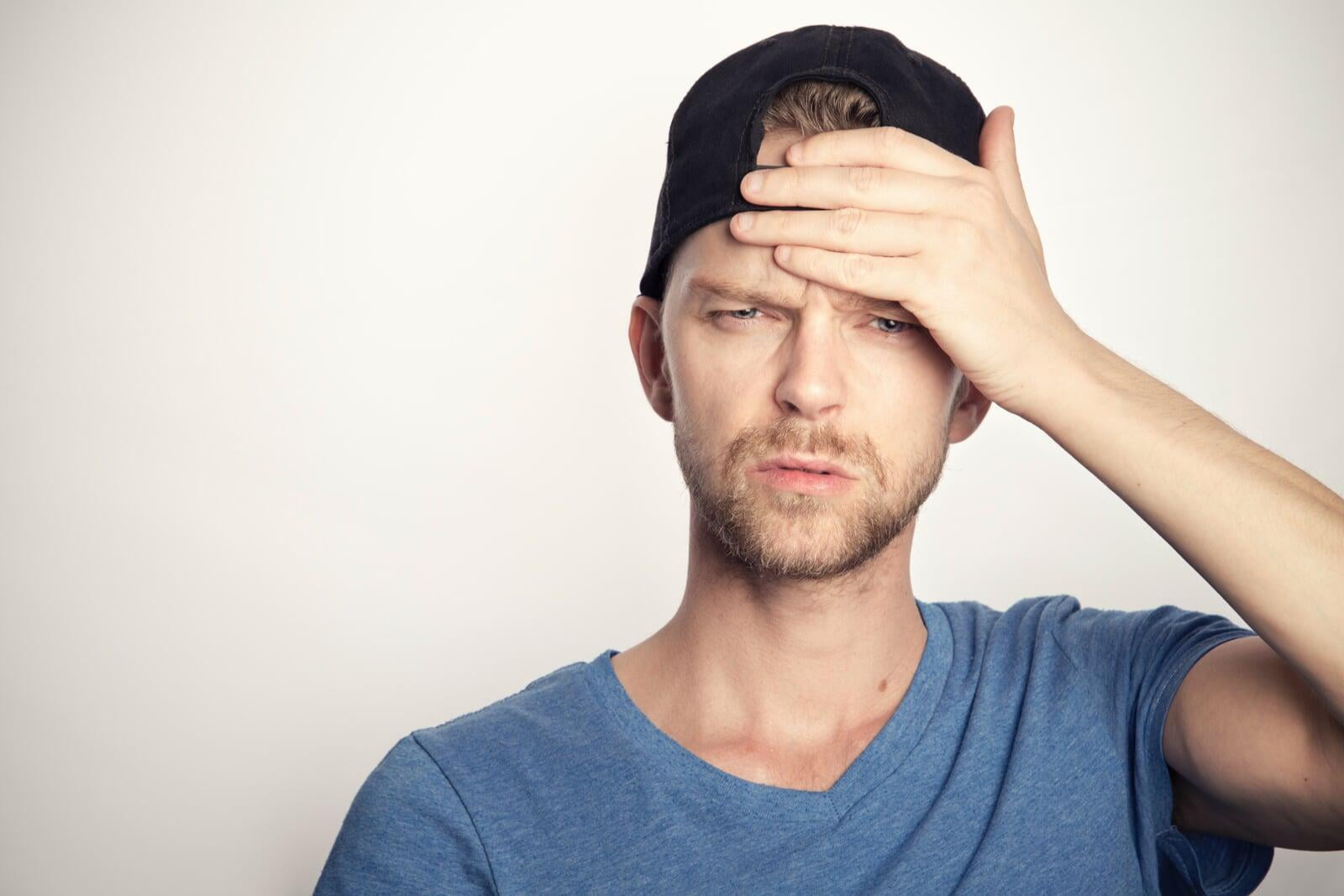
We'd like to introduce a fresh perspective on cost reduction while maintaining high-quality standards.
Imagine managing over 50 projects simultaneously across various product categories
plush toys, figurines, clothing, pins, and more. Different teams, multiple suppliers, designers,
finance, and logistics all play a role.
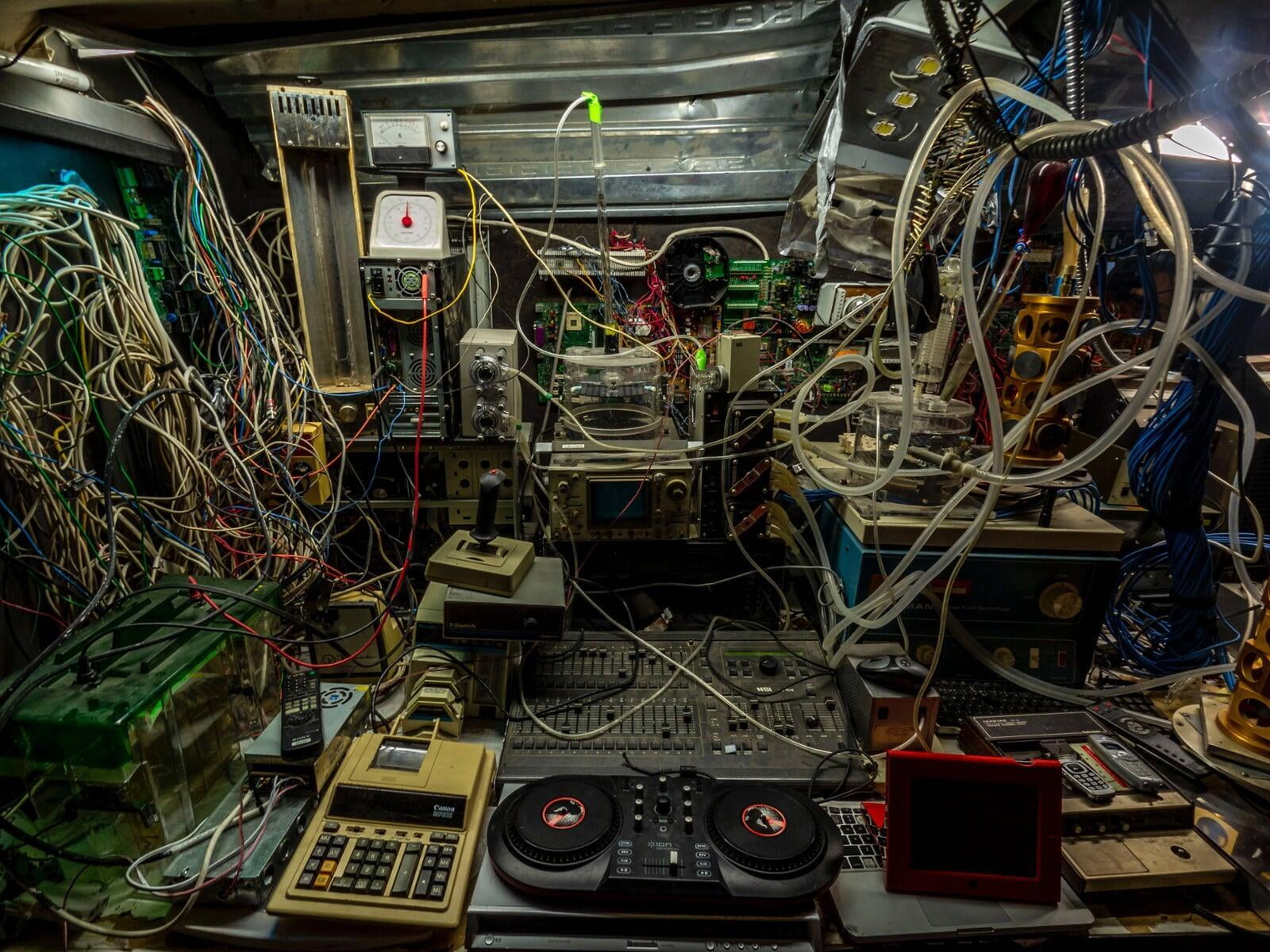
Now picture the information overload: design drawings,
product quotes, sample images, modification feedback, washing labels, purchase order details,
invoices—all scattered across emails, Google Drive, and other software. It’s like untangling a messy yarn ball, and if an
employee takes a break or leaves permanently (no blame there!), finding critical information becomes even harder.
The Traditional Factory Collaboration Process: Flaws and Challenges
1. Lack of Communication Efficiency:
People spend unnecessary time syncing information and resending files.
Vital details get lost in the shuffle, leading to confusion and delays.
2.No Big Picture View for Managers:
2.No Big Picture View for Managers:
Managers struggle to get a comprehensive overview of all ongoing projects.
This lack of visibility hampers effective production planning.
This lack of visibility hampers effective production planning.
3.Training and Handover Difficulties:
New employees require extensive training due to complex processes.
New employees require extensive training due to complex processes.
When someone leaves, knowledge transfer becomes a daunting task.
4.Tracking Issues and Mistakes:
4.Tracking Issues and Mistakes:
Without a streamlined system, mistakes increase.
Longer production times, project delays, and wasted manpower result.
Longer production times, project delays, and wasted manpower result.
The Solution: Enterprise Resource Planning (ERP) System
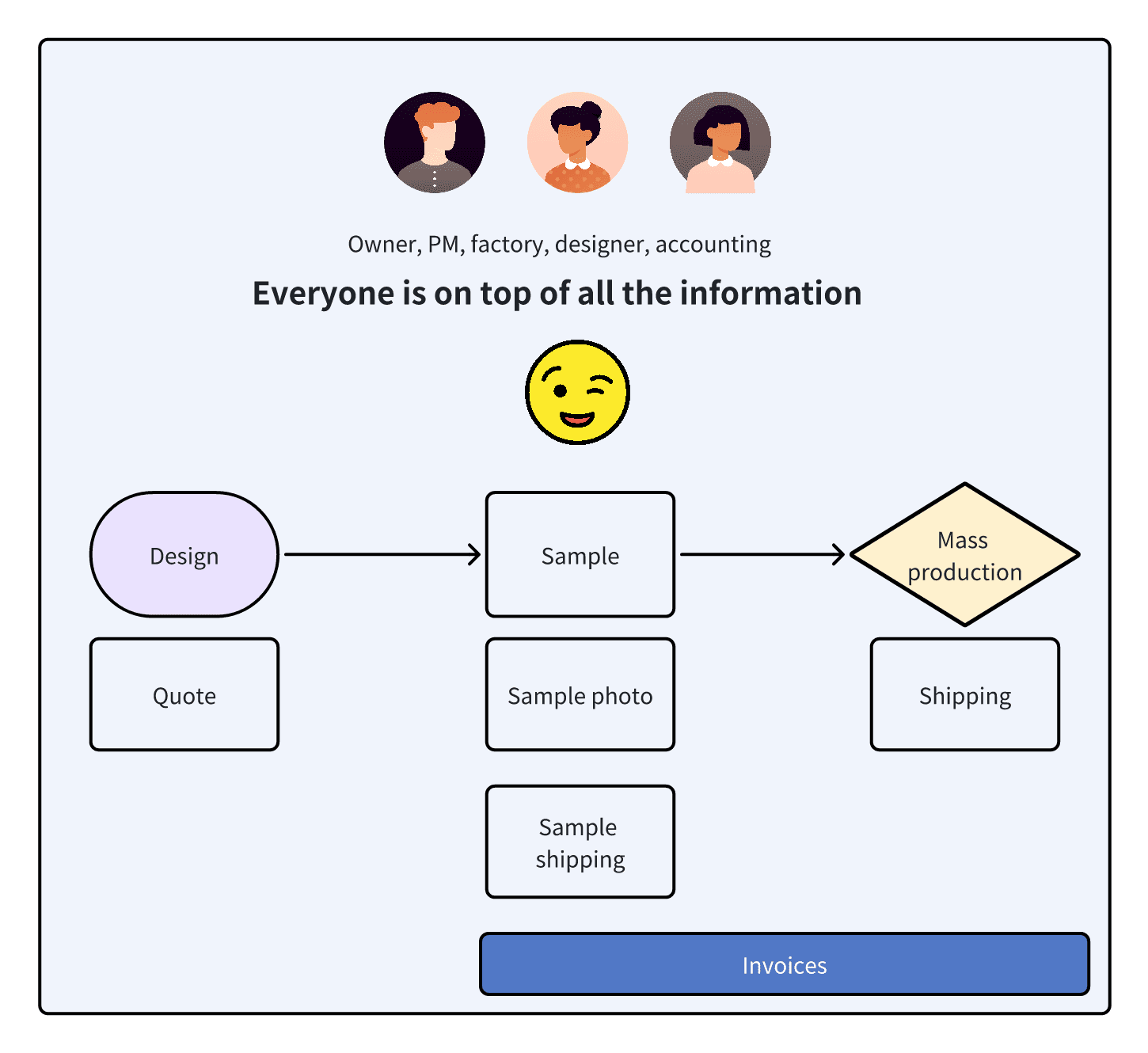
An ERP system streamlines communication across the entire production chain. Here’s how it works:
Sample Orders:
Each sample corresponds to a single page within the system.
This page contains design drawings, sample images, quotations, and other relevant details.
No more digging through scattered emails or folders!
Bulk Orders:
Similarly, each bulk order has its own dedicated page.
Details include product specifications, quantities, estimated delivery times, and more.
Managers can easily track progress and plan production efficiently.
Finance Integration:
Every sample and bulk order links to a corresponding invoice.
This simplifies verification and ensures accurate financial records.
Our Experience and Cost Savings
Our merch solution business has spent 7 years refining this system. We’ve digitized everything—
from client interactions to sample room management and production. The result? Significant cost savings—
at least $50,000 USD annually!
Get Started
If you’re interested in manufacturing merchandising items with us (such as plush toys, vinyl figures, or t-shirts),
our system is freely available. Feel free to reach out to us for more information or to explore our production catalog.
Remember, with the right system in place, you can save costs without compromising quality. Happy merchandising! 🛍️🌟